Understanding the **Automobile Parts Mold** Industry
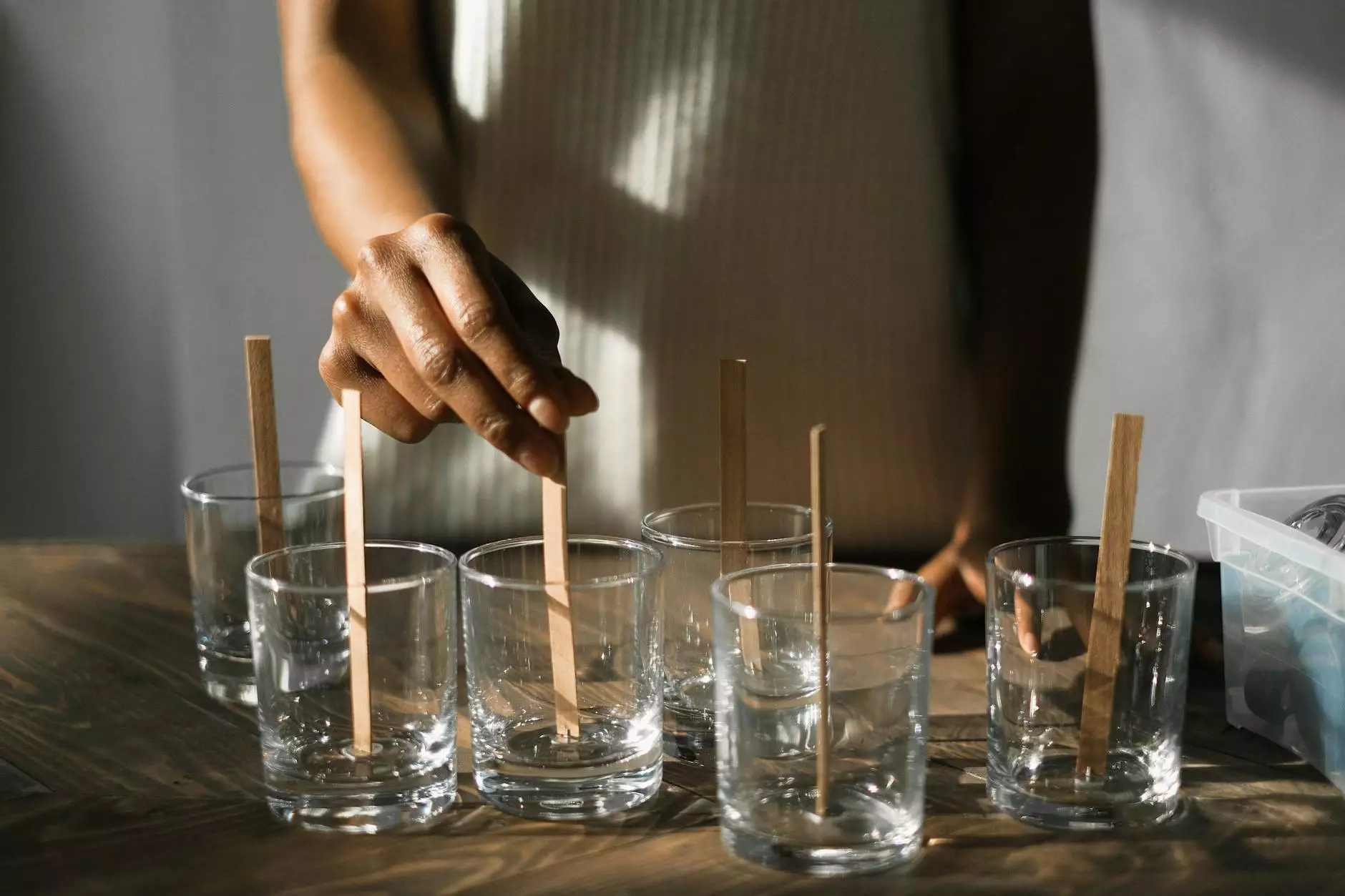
The automobile parts mold sector plays a crucial role in the automotive industry, ensuring that every vehicle is equipped with high-quality components. With the increasing demand for vehicles globally, the need for manufacturers to deliver dependable and efficient parts has never been greater. In this article, we will explore how companies like hanking-mould.com are setting benchmarks in quality and innovation in the field of plastic injection mould manufacturing.
The Importance of Automobile Parts Molds
Automobile parts molds are essential for producing a wide range of components that make up modern vehicles. This includes everything from the exterior body panels to intricate interior fittings and mechanical parts. Each component must meet stringent quality standards to ensure safety and longevity. The importance of employing skilled mold makers cannot be overstated. A well-crafted mold guarantees precise dimensions and tolerances, which directly influence the performance of the automotive parts.
Key Benefits of Quality Automobile Parts Molds
- Enhanced Precision: High-quality molds offer precise shapes and sizes, minimizing errors in component production.
- Cost Efficiency: Utilizing durable molds reduces wear and tear, leading to lower production costs over time.
- Improved Production Speed: Efficient molds allow for quicker cycle times, enhancing overall productivity.
- Reliability: Consistent quality leads to dependable vehicle parts, ensuring customer satisfaction.
Types of Automobile Parts Molds
Within the realm of automobile parts molds, various types exist to cater to different components of vehicles:
1. Injection Molds
Injection molds are widely used to manufacture plastic components. This process involves injecting molten plastic into a mold cavity. It is ideal for creating complex shapes with high accuracy.
2. Blow Molds
Blow molding is typically used for producing hollow plastic parts, such as fuel tanks and containers. This method involves inflating hot plastic within a mold to shape the final product.
3. Compression Molds
Compression molding is a technique where plastic is heated and then applied to a mold. This method is suitable for producing larger parts and ensures strong durability.
Choosing the Right Plastic Mold Maker
When selecting a plastic mold maker, several criteria should be considered to guarantee the best results:
1. Experience and Expertise
Choose a mold maker with substantial experience in the automotive sector. Knowledge of the specific requirements and industry standards is vital.
2. Technology and Equipment
Advanced machinery and technology are essential for producing high-quality molds. Ensure the manufacturer invests in the latest equipment.
3. Quality Assurance Procedures
A reputable mold maker should implement rigorous quality control processes to monitor every stage of production and guarantee excellence.
4. Customization Capabilities
Each automotive part has unique specifications. A good mold maker should be able to customize solutions to meet specific client needs.
Innovative Trends in Automobile Parts Molds
The industry is continually evolving, with new technologies and methodologies emerging to improve efficiency and product quality. Some exciting trends include:
1. 3D Printing Integration
3D printing is becoming a viable method for creating prototypes and even production parts. This technology allows for rapid prototyping of molds, enabling quicker iterations and adjustments.
2. Smart Manufacturing
The incorporation of IoT (Internet of Things) in manufacturing processes brings data analytics into mold production, optimizing performance and maintenance schedules.
3. Sustainable Practices
With rising environmental concerns, the automotive industry is shifting towards more sustainable practices, including using recycled materials in molds and reducing waste during production.
The Role of Plastic Injection Mould Manufacturer in the Automotive Sector
A plastic injection mould manufacturer is pivotal in ensuring that the molds are crafted precisely to the specifications required by automotive designers and engineers. Here’s how they contribute:
1. Creating Prototypes
Before mass production, manufacturers often develop prototypes to test functionality and fit. This step is crucial for identifying potential design flaws.
2. Consistency in Production
Once a mold is approved, maintaining consistency in every production run is essential. Quality manufacturers implement strict quality control measures to ensure that each part meets predetermined standards.
3. Collaboration with Designers
Close collaboration between mold makers and automotive designers ensures that the final product is both functional and innovative. Communication throughout the design and manufacturing processes enhances efficiency.
Conclusion: The Future of Automobile Parts Molds
The future of automobile parts molds is promising, with advancements in technology driving innovation and efficiency. As the automotive industry continues to evolve with new trends, the demand for high-quality molds produced by skilled manufacturers remains strong. Companies like hanking-mould.com are at the forefront of this revolution, providing quality solutions that keep pace with the needs of modern vehicles and their ever-demanding consumers. The commitment to excellence in production will ensure that they remain a trusted partner in the automotive supply chain.
FAQ about Automobile Parts Mold
1. What materials are commonly used in automobile parts molds?
Typically, materials such as steel and aluminum are used due to their durability and ability to withstand high-pressure conditions during production.
2. How long does it take to manufacture a mold for automobile parts?
The timeline can vary significantly based on complexity but typically ranges from a few weeks to several months.
3. Can molds be repaired if damaged?
Yes, many molds can be repaired, often extending their lifespan and functionality, but it depends on the extent of the damage.
4. What is the typical lifespan of an automobile parts mold?
The lifespan of a mold can vary widely, but with proper maintenance and care, molds can last for thousands of cycles, sometimes exceeding the lifespan of the project they were intended for.
5. What innovations should we expect in the future of automobile parts molds?
We anticipate advancements in biodegradable materials, improved energy-efficient manufacturing processes, and greater integration of AI and machine learning to optimize production workflows.