Custom Blade Manufacturing: Elevating Precision and Quality
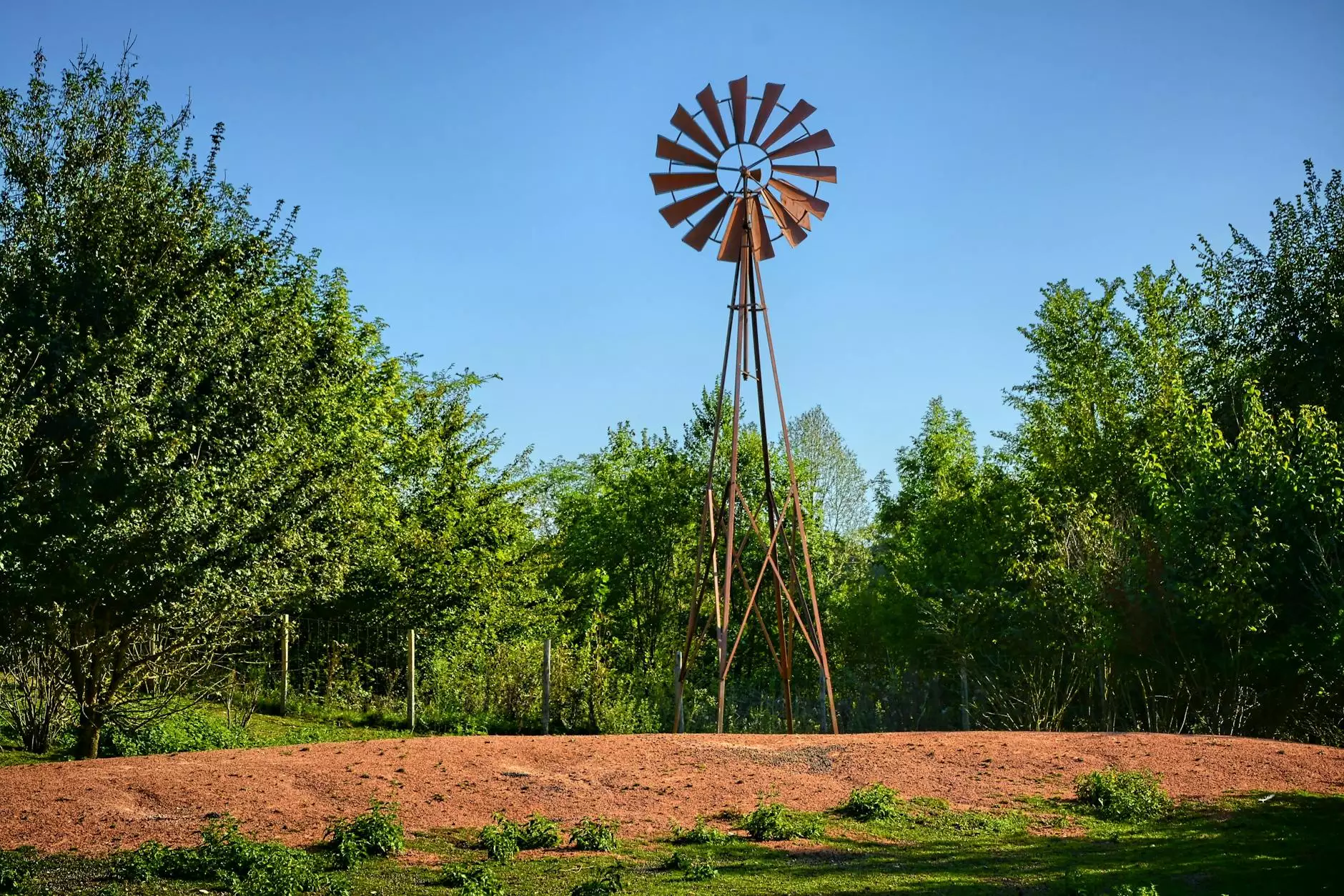
Custom blade manufacturing is an essential niche in the industrial and consumer market, serving a diverse range of needs across multiple industries. From specialty knives to precision cutting tools, the demand for quality blades has never been higher. Businesses like szblade.com are at the forefront of this demand, delivering customized solutions that exceed expectations.
The Importance of Custom Blade Manufacturing
In today’s fast-paced industrial environment, the necessity for bespoke solutions is paramount. Here’s a closer look at several factors driving the demand for custom blade manufacturing:
- Precision Engineering: Each application may require different specifications, such as blade thickness, material, and cutting edge design. Custom manufacturing allows for tailored solutions that guarantee the best performance for specific tasks.
- Material Selection: Comparing various materials such as stainless steel, carbon steel, or ceramic, businesses can select options that suit their needs for durability and performance.
- Cost-effectiveness: Investing in custom blades can reduce waste and increase efficiency, providing long-term savings for businesses.
- Brand Identity: Custom blades can incorporate unique designs or logos, helping businesses to stand out in a competitive market.
Key Characteristics of Quality Custom Blades
When it comes to custom blade manufacturing, a few characteristics define quality products:
1. Material Quality
The foundation of any blade lies in its material. Selecting the right material ensures that the blade can endure numerous cutting tasks and resist wear. Common materials used in blade manufacturing include:
- Stainless Steel: Known for its corrosion resistance and durability, stainless steel is a popular choice in many industries.
- High Carbon Steel: It offers superior sharpness and edge retention but demands regular maintenance to prevent rust.
- Ceramic: Lightweight and incredibly sharp, ceramic blades are often used for precision cutting tasks.
2. Edge Geometry
The shape of the blade’s edge is crucial to its cutting ability. Different edge configurations suit specific applications:
- Straight Edges: Ideal for slicing and fine cuts.
- Serrated Edges: Best for cutting through tougher materials.
- Curved Edges: Excellent for slicing and skinning.
3. Manufacturing Precision
Modern manufacturing techniques, such as CNC machining, enable unparalleled precision in creating custom blades. Precision ensures that each blade meets rigorous specifications, from thickness to sharpness.
Applications of Custom Blades
Custom blades find applications across a range of industries. Some notable uses include:
1. Culinary Berks
Professional chefs often require specialized knives tailored to their unique cooking styles. Custom blades can significantly improve efficiency and enhance culinary artistry.
2. Industrial Applications
In manufacturing and production, custom blades are used in machinery for cutting raw materials. They enable efficient production processes while maintaining the integrity of the material being worked on.
3. Woodworking and Carpentry
Custom blades are critical in tools such as saws and chisels, allowing carpenters to achieve precise cuts and finishes.